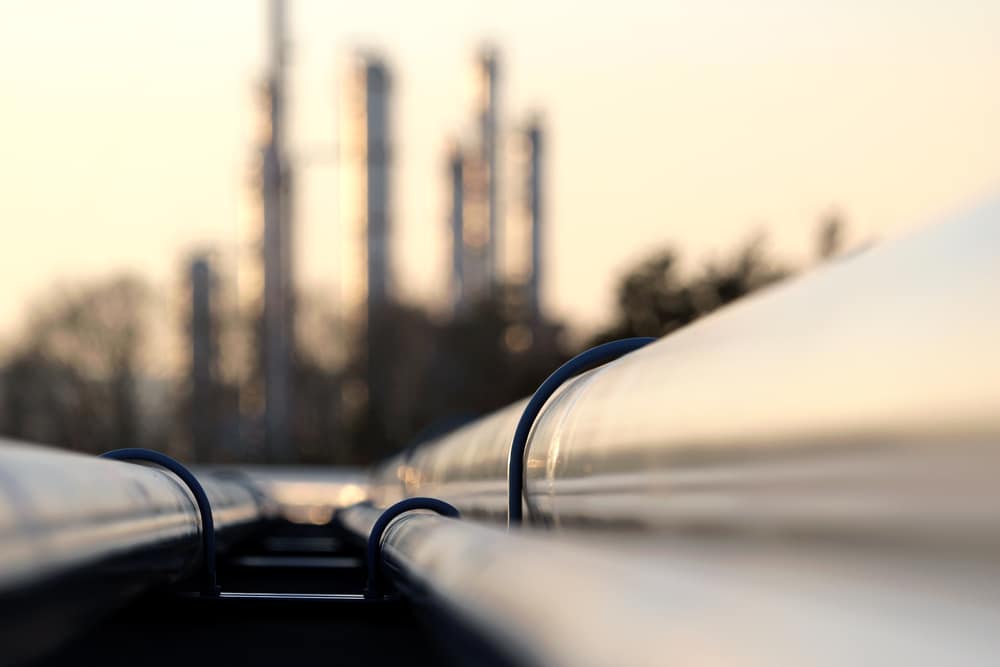
Steel pipes are an essential component in several industries including construction, infrastructure, and manufacturing. They can be used for a wide variety of applications, such as transporting liquids and gases, structural applications, and the oil and gas industry.
With so many possible uses, you may wonder how steel pipes are manufactured. So, here is an overview of the steps involved in manufacturing steel pipes.
1. Raw Material Selection
The first step in the manufacturing process of steel pipes is the selection of raw materials. As you could guess, the primary material used during this process is steel.
Steel is an alloy made from iron and carbon, with the carbon content in the steel being a large determinant in the strength and durability of the finished product.
It may also contain other materials like nickel, chromium, and molybdenum to improve specific properties of the product.
2. Heating & Rolling
Once the raw materials have been compiled, the next step is to heat and roll the steel into a cylindrical shape.
In order for this to occur, the steel must be heated to a temperature of around 2100-2400°F, then passed through a rolling mill. The rolling mill applies pressure to the steel, creating a cylindrical shape.
This process may be repeated many times until the desired thickness and diameter of the steel are achieved.
3. Welding
After the steel has been rolled into a cylindrical shape, the next step in the process is to weld the edges together to turn the curved metal into a usable steel pipe.
Two primary methods of welding can be used in the manufacturing of steel pipes:
- Electrical resistance welding (ERW)
- Submerged arc welding (SAW)
In the ERW method, the edges of the steel cylinder are heated and pressed together using an electrical current.
On the other hand, with the SAW method, the edges of the steel are heated using an electrical arc, then a layer of flux is applied to protect the weld from outside contamination.
4. Sizing & Cutting
With the welding step complete, manufacturers will move on to the next stage where they size and cut the pipe to their liking.
The steel pipe is passed through a series of sizing rollers that reduce the diameter of the pipe to the desired size. After this, the pipe is cut to the required length using a saw or torch.
5. Testing & Inspection
The final step in the manufacturing process is to test and inspect the pipes. Depending on the manufacturer, the steel pipe will undergo a series of tests to ensure that it meets the required specifications. Such tests can include hydrostatic testing, ultrasonic testing, and X-ray testing.
Once these tests are complete, the steel pipe can be inspected for any visible defects or imperfections. The pipe may be repaired or scrapped if any defects are found.
In sum, the manufacturing process for steel pipes is an intricate process that takes raw materials and turns them into functional components that are integral to our modern world. The versatility of steel pipes can be seen by their wide use across different industries, though this also means that the manufacturing process must be precise and accurate to ensure their reliability and strength.