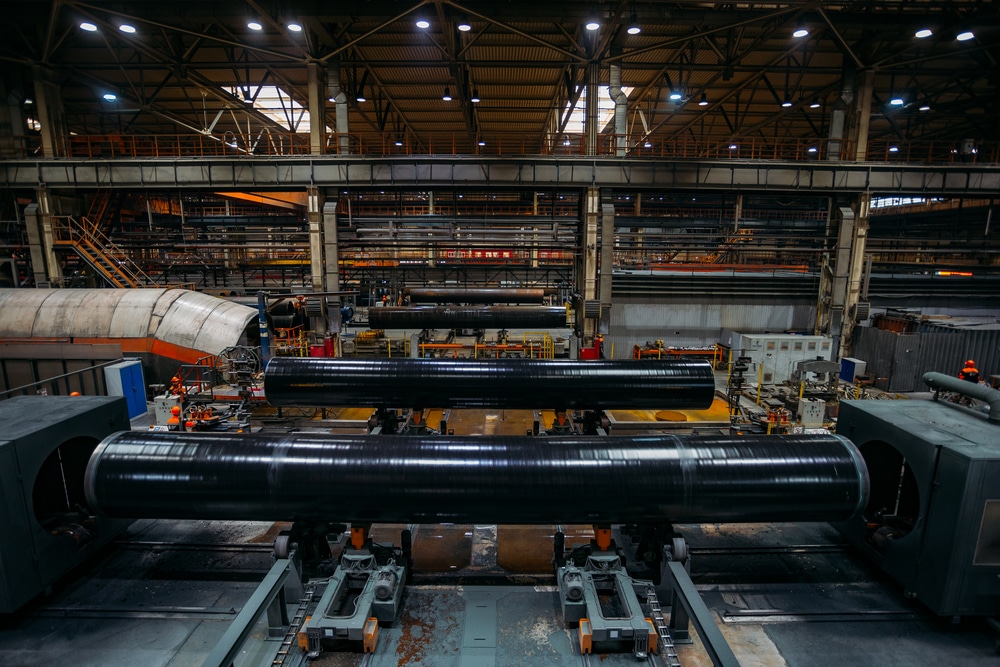
Many industries rely on steel pipes, valves, and connections to transport fluids and deliver other critical services. However, corrosion is often a major problem that they will face, which can cause significant damage to pipes and lead to costly repairs and replacements.
Fortunately, there are several methods of protecting pipes from corrosion, including coatings and linings.
Throughout this guide, we’ll focus specifically on Fusion Bonded Epoxy (FBE) coating, a highly effective and popular method of protecting pipes from corrosion–including what it is, how it works, and when it is needed.
What is FBE Coating
Fusion Bonded Epoxy (FBE) coating, sometimes referred to as powder coating, is a thermosetting resin coating that’s applied to steel pipes and is considered to be the industry standard for industries like oil and gas, water, sewage, and more.
FBE coating gets applied to both the exterior and interior of the pipe and is a highly effective method of protecting the pipe from corrosion.
When is FBE Coating Utilized?
FBE coating is needed for pipes that are exposed to harsh environments, like those that come into contact with salt water, chemicals, and other corrosive materials.
It is also used to protect pipes that are buried underground where they are subject to corrosion from soil and moisture.
This type of coating is highly effective in protecting pipes from corrosion, abrasion, and chemical attack, which can cause costly damage and reduce the lifespan of the pipe. FBE coating can also help to improve the flow of fluid through the pipe by reducing friction and turbulence.
In addition to its protective properties, FBE coating is also environmentally friendly and can be applied without emitting any harmful substances. This makes it a popular choice for many industries that prioritize sustainability and environmental stewardship.
How is FBE Coating Applied?
The FBE coating process involves applying an electrically charged epoxy powder to the heated pipe, which then melts and fuses to the surface. But before this is done, the pipe surface is cleaned and heated to ensure proper adhesion. In many cases, the pipe will be heated from 350-500° F during this process.
The result is a strong, durable, and uniform coating that provides superior corrosion resistance and prevents the pipe from deteriorating over time.
The fusion bonding that takes place throughout this process means the coating is irreversible and cannot return to its original form of powder, even upon further heating of the pipe. This means the coating will not melt even under extreme conditions.
FBE Coating Alternatives
There are some alternatives to steel pipe coating aside from FBE coating, including:
- 3-Layer Polyethylene (3LPE) Coating
- Polyurethane (PU) Coating
- Coat Tar Enamel (CTE) Coating
- Zinc Coating
Each method has its own advantages and disadvantages, and the choice between these options will come down to the specific application and level of corrosion protection needed. So, you may want to consult with a corrosion expert to find the best coating for you based on the fluids being transported, the conditions the pipe will be exposed to, and other factors.
Overall, FBE coating is a highly effective method of protecting pipes from corrosion and damage. In turn, this can extend the life of the pipe and reduce the need for costly repairs and replacements. Because of this, it’s a popular choice in several industries that require reliable and durable piping systems, including oil and gas, water, and sewage.